Ethical Manufacture
Sedex approved
Ethical garment manufacturing is offered with our partner factory NUAS in Sri Lanka; a Smeta(Sedex) fully accredited 4 pillar factory that adheres to stringent standards. This ensures Fair Labour standards, no forced or child labour and that working conditions are safe and hygienic.
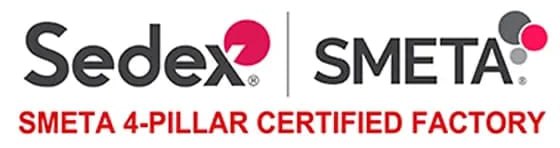
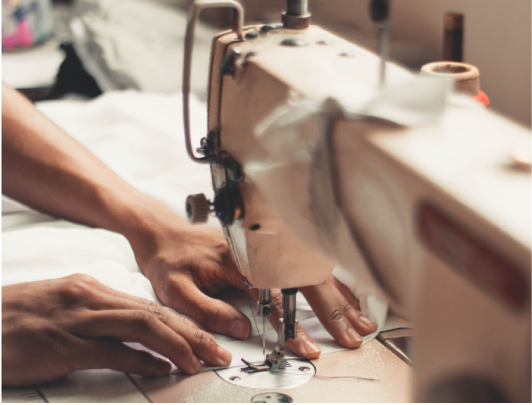
Fair Labour standards
Fair living wages are paid to all workers with workers paid 20% above minimum wage. Working hours of workers are not excessive, strictly adhering to a 45 hour working week, with over time paid at double pay and additional holiday. Regular employment is provided to all employees. We have a zero tolerance of harsh or inhuman treatment to workers or any form of discrimination.
Order quantities are flexible from 150 units per style with a monthly production capacity of 80,000 units. Offering fully integrated vertical supply of regenerative, organic, recycled & biodegradable fabrics. Our team of industry professionals manage services from design to delivery offering sustainable solutions throughout.
FULLY TRACEABLE
Ethical Manufacturing
A high degree of environmental standards are maintained with compliance of all local and national laws for all manufacturing processes. Our garment manufacturing maintains the highest degree in business conduct with stable working environments. Workers are provided with free meals, free medical facilities and free transport facilities. Offering complete transparency of pricing and supply chain. Workers are provided with:
- 20 % + above minimum wage
- Free meals, transport and medical facilities
- Strictly 45 hours per week with compensated overtime at double pay
- Workers council representing fair communication with management
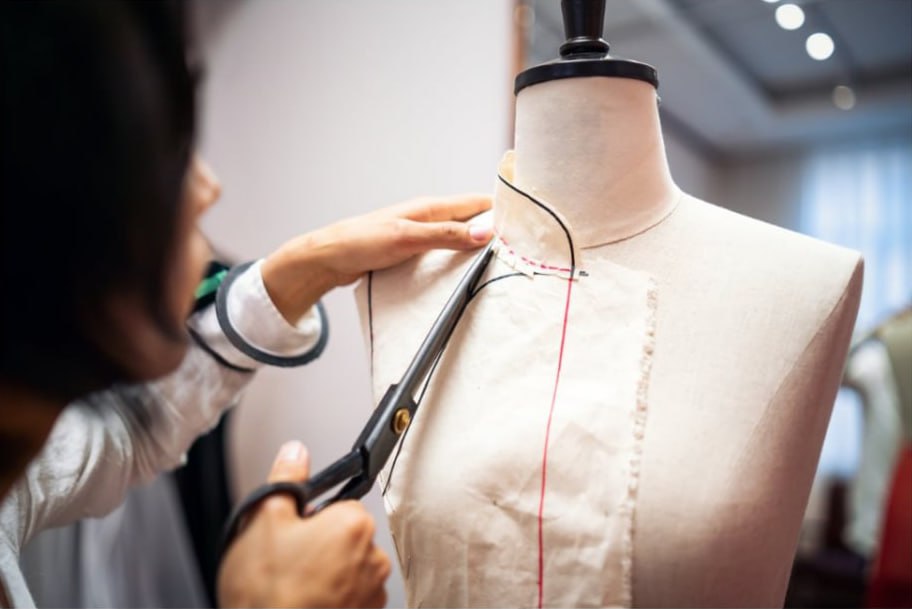
SERVICES
- Design development, 3D prototyping, sampling, production
- Fully traceable supply of regenerative cotton
- Expertise in sourcing sustainable fabrics and trims
- 60 – 80,000 units p.c.m garment production capacity with flexible M0Q’s
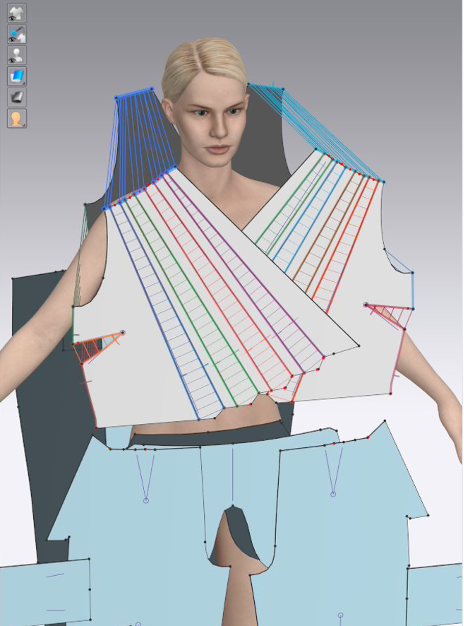
DIGITAL EFFICIENCY
Rapid 3D Prototyping.
We offer digital CLO 3D technology, improving efficiency in the garment development process. 3D prototyping creates a faster sample development process and on average requires 50% less samples. This saves time, cost, material waste and transport costs, further reducing carbon footprint.
Edits can be made on a virtual sample in real time, instead of producing multiple iterations of physical samples. Technical designers can check for fit issues earlier on, identifying solutions to adjust and update measurements.
Virtual sampling changes the sampling landscape, offering a dynamic way to either adapt existing patterns to instantly see how those 2D iterations look, or to work with improved efficiency to meet deadlines.
Digital prototyping makes collaboration easier, improving communication throughout the supply chain and is a valuable tool to be leveraged in the apparel design process.
CARBON FOOTPRINT
Regenerating land through natural farming to restore soil health and sequester carbon from the atmosphere.
WATER FOOTPRINT
Reducing water footprint through rain- fed irrigation. Preventing chemicals from entering water cycle by removing from agricultural and textile processes.
CLEAN TEXTILES
From non GMO seed to natural fibre. Chemical free cotton fabric grown regeneratively free of herbicides and pesticides.
SOCIAL IMPACT
Increasing Farmer Incomes With A Focus On Tribal Women Farmers supporting better livelihoods.
TRACEABLE
Fully traceable with complete transparency from seed to sewn garment, establishing a direct relationship with your organic cotton supply.
VALUE PARTNERS
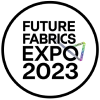
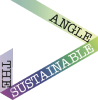
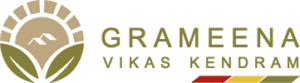
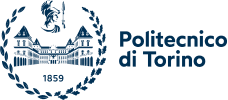
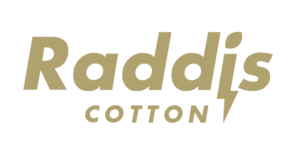